Concrete and Polished Concrete
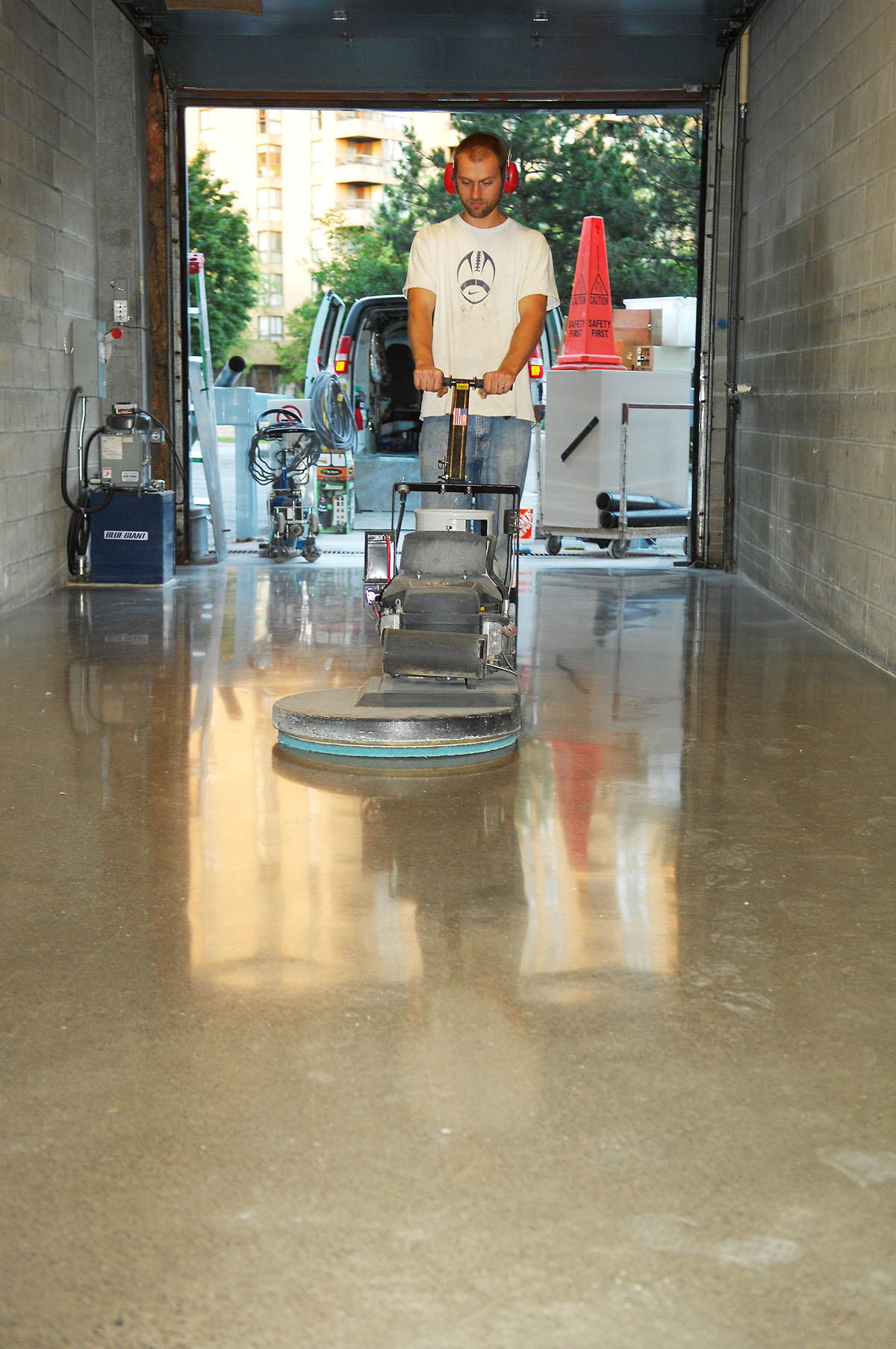
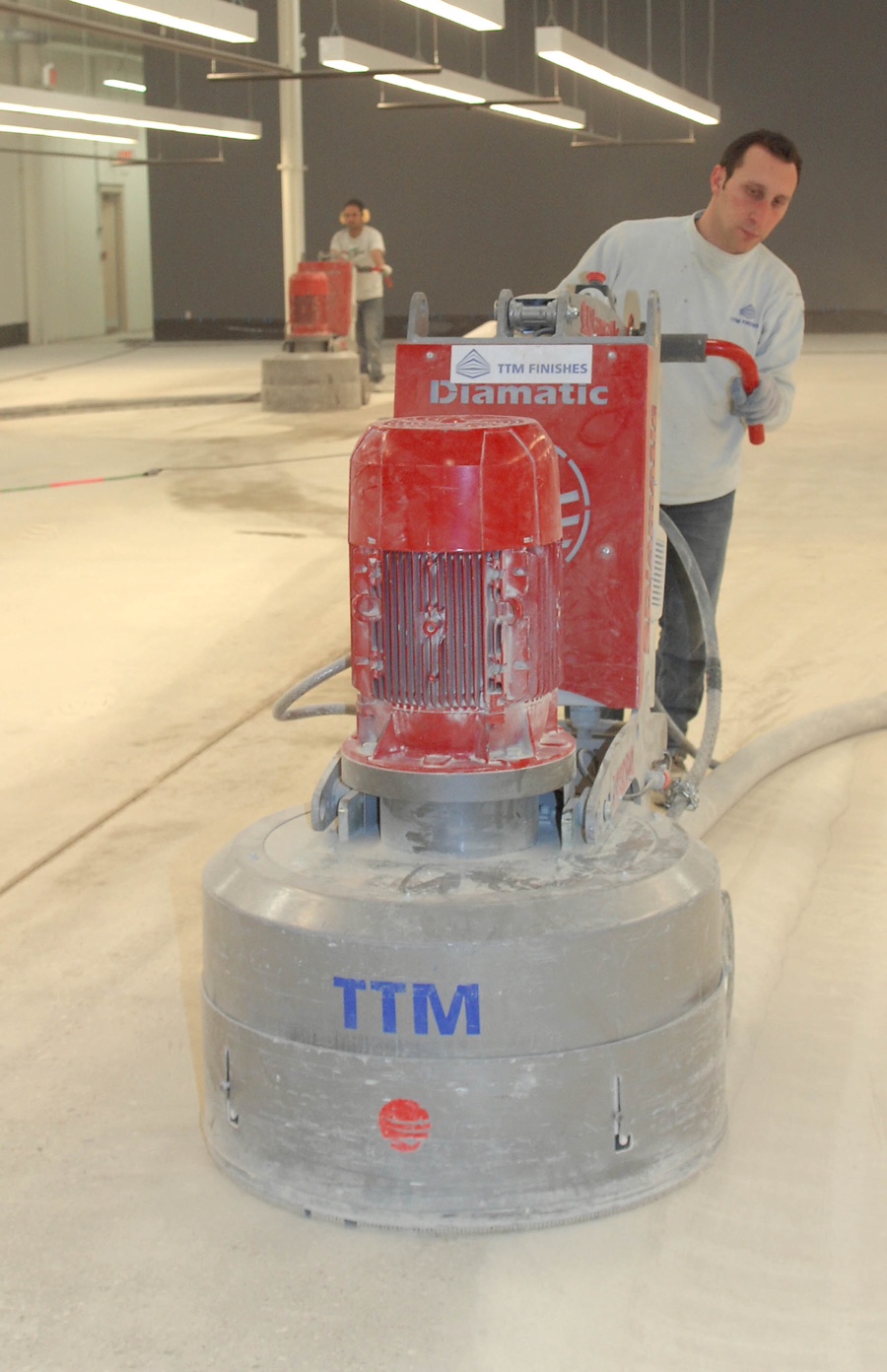
A. Concrete Basics
The most common substrate for commercial and residential floors is concrete. Some people refer to the floor as "cement" rather than concrete, which is technically and terminologically incorrect as cement is one of the ingredients used to make concrete.
Concrete is comprised, in its most basic form, of Portland cement, gravel, sand and water. Admixtures (concrete additives), which are ingredients added before or during the mixing of concrete, may be also used to enhance certain qualities such as to improve the strength of the concrete, to reduce the water demand in the concrete mixes, to speed up or slow down the set-up time, and to help protect concrete against the effects of temperature changes and exposure to chemicals such as deicers. The Portland cement powder reacts with water through a chemical reaction called "hydration" to form a paste, which acts as the basic glue that holds the sand, gravel and other components together. The key to achieving a strong, durable concrete depends heavily on the cement/water ratio as well as the proportions of other ingredients. Generally, using less water produces a higher quality concrete provided the concrete is properly placed, consolidated, and cured. Typical, concrete mixture consists of:
5-8% Entrained air
11-15% Portland cement
15-20% Water
35-45% Gravel or crushed stone
25-30% sand (fine aggregate)
Slump: is the term used to describe the consistency, stiffness and workability of fresh concrete. The results of a slump test are stated in inches. It is influenced by the amount of water in fresh concrete. More water means a higher slump, but water is not the only influence. Admixtures can be used to increase slump without increasing the water in the concrete. The type of aggregate, the air content, the admixtures, the temperature and the proportions of all the ingredients have an effect on slump. The typical slump used for external flatwork is 4-5 inches. High quality external concrete would have slump of 2 to 4 inches.
Compressive Strength: A pound per square inch (psi) is the unit of measurement used to describe the compressive strength of concrete. The most desirable strength for external concrete slabs varies based on climatic conditions. In broad terms, the colder the climate, the higher the desired psi. Areas which experience large numbers of freeze and thaw cycles also require a higher psi concrete mix design.
INGREDIENTS:
1. Portland Cement
They are different types of Portland cements that are manufactured to meet various physical and chemical requirements. The most common one is Type I Portland cement, which is the general-purpose cement. There are other cement types available, including white Portland cement, which is identical to gray Portland cement in every aspect but color. White Portland cement contains only negligible amounts of iron and magnesium oxides, the substances that give gray cement its color. It is used generally whenever architectural considerations specify white or colored concrete or mortar.
They are many type of concrete. By far the most common form is "ready mixed concrete" which accounts for nearly three-fourths of all concrete used in the market. It's batched at local plants for delivery in the familiar trucks with revolving drums.
2. Water
Water is a necessary ingredient in the making of concrete. When water is blended with cement, the hydration reaction takes place leading to the formation of cement paste. The correct amount of water causes the microscopic crystals of cement to react, absorbing water in the process, growing closer together to hold the sand and aggregate more tightly together. As the reaction progresses, the cement paste will gradually begin to stiffen and harden until it ultimately sets. It is known as "green concrete" at this point. The amount of water added to make a good concrete mix is a compromise between strength and workability. Excess water causes the crystals to grow farther apart and causes the concrete to lose its thick, syrupy consistency, resulting in it becoming soupy. In this case, the aggregate sinks to the bottom and cement rises to the top resulting in a weak concrete. A mix that's too wet will also cause the surface to shrink excessively, crack and chip off.
Almost any natural water (drinkable and otherwise) may be used as mixing water for concrete as long as it does not have a high level of impurities that may affect setting time and concrete strength. Impurities may cause efflorescence, staining, corrosion of reinforcement, volume instability, and reduced durability.
3.Aggregates
Aggregates are inert granular materials such as sand, gravel, or crushed stone that, along with water and Portland cement, are an essential ingredient in concrete. Aggregates comprise 60 to 75 percent of the total volume of concrete and must be chosen carefully. The type and size of the aggregate mixture depends on the thickness and purpose of the final concrete product. A continuous gradation of particle sizes is desirable for efficient use of the paste.
For a good concrete mix, aggregates need to be clean, hard, strong particles, free of absorbed chemicals or coatings of clay and other fine materials that could cause the deterioration of concrete. Aggregates are divided into two distinct categories: fine and coarse. Fine aggregates generally consist of natural sand or crushed stone with most particles passing through a 3/8-inch (9.5-mm) sieve. Coarse aggregates generally range between 3/8 and 1.5 inches (9.5 mm to 37.5 mm) in diameter. Gravels constitute the majority of coarse aggregate used in concrete with crushed stone making up most of the remainder. Natural gravel and sand are usually dug or dredged from a pit, river, lake, or seabed. Crushed aggregate is produced by crushing quarry rock, boulders, cobbles, or large-size gravel. Recycled concrete is a viable source of aggregate as well. Aggregate processing consists of crushing, screening, and washing the aggregate to obtain proper cleanliness and gradation. Once processed, the aggregates are handled and stored in a way that minimizes wetting, segregation and degradation and prevents contamination. Aggregates strongly influence concrete's freshly mixed and hardened properties, mixture proportions, and economy. The most important characteristics that are considered when selecting aggregate include:
a) Grading refers to the determination of the particle-size distribution for aggregate. Grading limits and maximum aggregate size are specified because grading and size affect the amount of aggregate used as well as cement and water requirements, workability, pumpability, and durability of concrete.
b) Particle shape and surface texture influences the properties of freshly mixed concrete more than the properties of hardened concrete. Rough-textured, angular, and elongated particles require more water to produce workable concrete than smooth, rounded compact aggregates. Consequently, the cement content must also be increased to maintain the water-cement ratio. Generally, flat and elongated particles are avoided or are limited to about 15 percent by weight of the total aggregate.
c) Unit-weights & voids are important factors when selecting aggregate. Unit-weights measure the volume that graded aggregate and the voids between them will occupy in concrete. The void content between particles affects the amount of cement paste required for the mix. Angular aggregate increases the void content. Larger sizes of well-graded aggregate and improved grading decreases the void content.
d) Absorption and surface moisture of aggregate are measured when selecting it because the internal structure of aggregate is made up of solid materials and voids that may or may not contain water. The amount of water in the concrete mixture must be adjusted to include the moisture conditions of the aggregate.
e) Abrasion and skid resistance of an aggregate are essential when the aggregate is to be used in concrete constantly subject to abrasion as in heavy-duty floors or pavements. Different minerals in the aggregate wear and polish at different rates. Harder aggregate can be selected in highly abrasive conditions to minimize wear.
4. Chemical Admixtures
Chemical admixtures are the ingredients in concrete other than Portland cement, water, and aggregate that is added to the mix immediately before or during mixing. Admixtures are used primarily to modify the properties of hardened concrete. Most admixtures are supplied in ready-to-use liquid form and are added to the concrete at the producer plant or at the jobsite. The effectiveness of an admixture depends on several factors including: type and amount of cement, water content, mixing time, slump, and temperatures of the concrete and air. There are 6 different ways that the admixtures contribute to the concrete quality.
- Air-entraining admixtures are introduced to the concrete mixture to purposely induce microscopic air bubbles into the exterior concrete slabs. Air entrainment helps protect exterior exposed concrete that will be subject to freezing, thawing and deicers. Air-entrained concrete contains billions of microscopic air cells. These relieve internal pressure on the concrete by providing tiny chambers for the expansion of water when it freezes. The amount of entrained air is usually between 5 percent and 8 percent of the volume of the concrete, but may be varied as required by special conditions. The use of air-entraining agents results in concrete that is highly resistant to severe frost action and cycles of wetting and drying or freezing, and thawing and has a high degree of workability & durability. Entrained air in hardened concrete dramatically reduces the scaling that might otherwise result from the use of chemicals to melt ice on roads and streets. It also prevents damage to pavements caused by freezing and thawing. The air bubbles function as minute safety valves by providing room for the free water in concrete to expand harmlessly as freezing occurs. If a concrete slab is to be protected by impervious overlay such as epoxy, air-entraining admixtures should not be used.
- Water-reducing admixtures usually reduce the required water content for a concrete mixture by about 5 to 10 percent. Consequently, concrete containing a water-reducing admixture needs less water to reach a required slump than untreated concrete. The treated concrete can have a lower water-cement ratio. This usually indicates that a higher strength concrete can be produced without increasing the amount of cement. Recent advancements in admixture technology have led to the development of mid-range water reducers. These admixtures reduce water content by at least 8 percent.
- Retarding admixtures, which slow the setting rate of concrete, are used to counteract the accelerating effect of hot weather on concrete setting. High temperatures often cause an increased rate of hardening which makes placing and finishing difficult. Retarders keep concrete workable during placement and delay the initial set of concrete. Most retarders also function as water reducers and may entrain some air in concrete.
- Accelerating admixtures increase the rate of early strength development; reduce the time required for proper curing and protection, and speed up the start of finishing operations. Accelerating admixtures are especially useful for modifying the properties of concrete in cold weather.
- Super-plasticizers, also known as plasticizers or high-range water reducers (HRWR), reduce water content by 12 to 30 percent and can be added to concrete with a low-to-normal slump and water-cement ratio to make high-slump flowing concrete. Flowing concrete (self leveling) is a highly fluid but workable concrete that can be placed with little or no vibration or compaction.
- Corrosion-inhibiting admixtures are used to slow corrosion of reinforcing steel in concrete. Corrosion inhibitors can be used as a defensive strategy for concrete structures, such as marine facilities, highway bridges, and parking garages, that will be exposed to high concentrations of chloride.
B. How to construct concrete floor?
Step 1: Preparation of the base:
Concrete floor is constructed by pouring and finishing concrete on a prepared base. The foundation of this base must be strong enough to support the intended weight.
a) Sub Grade Preparation:
Topsoil and organic matter should be removed. A granular base (stone or sand) may be necessary, and filled materials must be compacted uniformly. Because "flat" pavements can collect water, the sub grade should be sloped. At the time concrete is placed, the sub grade should be sprayed with water so that it is moist but not muddy. Depending on the local conditions, either the soil is compacted or a mixture of fine and coarse aggregates is placed on top of the local soil and compacted.
b) The Vapor Barrier:
A vapor barrier system is installed over the portion of the prepared ground where the slab is poured. The vapor barrier system is an impervious material of polyethylene sheeting that is overlapped and sealed. The purpose of the vapor barrier is to prevent the concrete from curling up at its edges during curing and drying. The barrier provides a more uniform release of the excess water. It also prevents water from entering the slab from beneath, which can cause osmotic blistering in the flooring material when it is installed on the top of the concrete. A dry sand layer is then put on top of the vapor barrier.
c) Reinforcement:
Concrete used in most construction work is reinforced with steel, particularly in applications subject to high tensile stresses. Steel is embedded in the concrete in the form of a mesh, wire fabric, or roughened or twisted bars. A bond forms between the steel and the concrete, and stresses can be transferred between both components.
Step 2: Pouring the concrete:
Concrete is poured into place in a number of ways. For the footings of small buildings, the wet concrete is poured directly into trenches dug into the earth below frost level. Concrete for foundations and certain types of walls is placed between supporting wood or metal forms, which are removed after the concrete has hardened. In lift-slab construction, floors and roof slabs are cast at ground level and then raised by hydraulic jacks and fastened to columns at the desired elevation. Slip forms are used to produce vertical shafts for silos and the cores of buildings. They are moved upward at a rate of 15 to 38 cm (6 to 15 in) per hour while concrete and reinforcements are put in place. The tilt-up method of construction is frequently used for one- and two-story buildings. Walls are cast in place on the ground or on the previously laid concrete floor and tilted into position by cranes. The walls are joined at the corners or between panels with cast-in-place concrete columns. To pave a highway or road with concrete, a slip-form paver is used. Two metal side forms are connected to a slip-form paver. A layer of concrete is poured between the side forms as the paver slowly moves forward on its treads; the side forms keep the concrete in position as it dries. Slip-form pavers can lay continuous strips of one or two lanes of concrete pavement.
For certain applications, such as the construction of swimming pools, canal linings, and curved surfaces, concrete may be applied by the shot crete method. In shot creting, concrete is sprayed under pneumatic pressure rather than placed between forms. Often the use of shot crete eliminates the need for formwork and permits placement of concrete in confined areas where conventional forms would be difficult or impossible to construct.
Step 3: Consolidation:
Once the concrete is thoroughly mixed and workable, it should be placed in forms (prepared base) as soon as possible before the mixture becomes too stiff. During placement, the concrete is consolidated to compact it within the forms and to eliminate potential flaws such as honeycombs and air pockets. It should not remove significant amounts of intentionally entrained air. Vibration, either internal or external, is the most widely used method for consolidating concrete. When concrete is vibrated, the internal friction between the aggregate particles is temporarily destroyed and the concrete behaves like a liquid; it settles in the forms under the action of gravity and the large entrapped air voids rise more easily to the surface. Internal friction is re-established as soon as vibration stops. Finishing must be delayed until water sheen has disappeared from the surface, then a wood or metal hand float is used to smooth off the concrete so that none of the aggregate particles are sticking out of the concrete. Floating produces a relatively even, but slightly rough, texture that has good slip resistance and is frequently used as a final finish for exterior slabs. If a smooth, hard, dense surface is required, floating is followed by steel troweling. Care must be taken to avoid adding water or overwork the surface. A broom finish is recommended for exterior concrete, except when special textured finishes (like exposed aggregate, stamped or impressed finishes) are desired. In hot weather, fresh concrete should be protected from the sun and wind-- even before it is finished. A surface evaporation retarder is one way to protect concrete in hot weather. Concrete can also be safely placed in cold weather when proper precautions are taken.
Step 4: Curing of the Concrete:
After concrete is placed, satisfactory moisture content and temperature (between 50°F and 75°F) must be maintained, a process called curing. Adequate curing is vital to quality concrete. Curing has a strong influence on the properties of hardened concrete such as durability, strength, water-tightness, abrasion resistance, volume stability, and resistance to freezing, thawing and deicer salts. During this step, it is very important that water be kept in the concrete during early stages because it is needed to react with Portland cement to form the binder. Curing ensures the continued hydration of the cement and the strength gain of the concrete. Various methods are used to prevent the loss of moisture from the concrete. Concrete surfaces are cured by sprinkling with water fog, or by using moisture-retaining fabrics such as burlap or cotton mats. Other curing methods prevent evaporation of the water by sealing the surface with plastic or special sprays (curing compounds). However, the most common methods are spraying concrete "curing & sealing compounds" onto the surface immediately after the final finishing to slow down evaporation, and keeping the concrete moist with water. They are typically made of chlorinated rubber, styrene acrylic solution. A cure and seal compound with ultraviolet (UV) protection is recommended for exterior applications to keep the concrete slab from generating a yellow tint. Generally, concrete should cure 3 to 7 days before being put in service.
The concrete must be dried after the initial curing is complete. The longer the concrete is kept moist, the stronger and more durable it will become. If temperatures are favorable, hydration is relatively rapid for the first few days after concrete is placed. Most of the hydration and strength gain take place within the first month of concrete's life cycle, but hydration continues at a slower rate for many years. Concrete continues to get stronger as it gets older. Most specifications for concrete have a 28-day minimum requirement. The amount of water added to the concrete is far in excess of the water needed for the hydration reactions. Any excess water must be allowed to escape before any impervious material such as coating, tiles, epoxy terrazzo, epoxy coating, carpeting and so on can be applied; failure to do so could cause severe osmotic blistering and lifting. The amount of time it takes for the water to evaporate from the slab depends on many variables such as thickness of the slab, water-to-cement ratio of the concrete, air temperature, concrete temperature, relative humidity and wind speed. It may take 60 days or more before the floor is ready to be coated. Exposed slab surfaces are especially sensitive to curing. Surface strength development can be reduced significantly when curing is defective.
C. Protective Coating for Concrete:
Concrete floor has many advantages, including its strength, hard-wear, and affordability, as well as being unaffected by heat or sun. The major drawbacks are that it is dusty, absorbent, noisy, difficult to clean, unattractive, brittle, easily contaminated by oil, and attacked by acids. To overcome these shortcomings, concrete floors are coated to improve aesthetics, light reflection, ease of cleaning, and protection from chemicals, oil or contaminants. Among all different types of coatings available in the market, two-part epoxy systems are by far the most effective technology for concrete protection.
Moisture Level in Concrete:
The movement of concrete slabs is commonly referred to as the "moisture vapor transmission rate". There are various methods for determining it in order to ensure susceptibility of the concrete floor to receive the coating system. The most commonly used method is the plastic sheet test as follows:
Standard Test for Indicating Moisture in Concrete (Using Plastic Sheet) (ASTM D 4263)
This test method is used to indicate the presence of capillary moisture in concrete. The capillary moisture in the concrete may be detrimental to the performance of impervious epoxy coating. The test method should be used prior to the application of coatings on concrete. This test method should be conducted when the surface temperature and ambient conditions are within the range established for the application of the coating. Avoid direct sunlight, heat or damage to the plastic sheet.
Materials:
- Transparent Polyethylene sheet , approximately 4 mils (0.1 mm) thick
- Adhesive Duct tape 2 in. (50mm) wide
Procedure:
- Tape a segment approximately 18 by 18 in. (457 by 457 mm) of transparent polyethylene sheeting material, tightly to the concrete surface making sure that all edges are sealed
- Allow the plastic sheet to remain in place for a minimum of 16 hours.
- After the allowed time has elapsed, remove the plastic sheet and visually inspect the underside of the sheet and the concrete surface of the patch for presence of moisture
Conclusion:
This test method indicates the presence of capillary moisture. This method is purely qualitative. Any signs of moisture on the underside of the sheet or on the floor (as evidenced by a darker grey color) mean that moisture is moving through the concrete, and the concrete is not ready for coating.
Surface Preparation of the Concrete Floor:
1. Laitance:
The surface of new concrete is weak, even on good high-strength concrete. This is because the vibration and troweling movements made when placing the concrete encourage the lighter components such as surplus Portland cement and water to rise to the surface. When this sets, it is called "laitance". It is present to a depth of approximately 0.05". This layer should be removed as described below.
2. Curing Compounds:
Curing compounds are often sprayed onto the concrete to act as a membrane to retard water evaporation while the concrete is curing. They must be removed before any subsequent coating is applied.
3. Pre-cleaning
All heavy deposits of dirt, asphalt, oil or grease must be removed before the final surface preparation. The best way of removing such deposits is by mechanical means, aided by grease cutting detergents. If solvent is used, care must be taken so the use of each solvent does not spread the contaminant over a larger area. To test the level of oil contaminant, a drop of water is placed on the surface. If it beads, an oil contaminant is present. It is essential to remove oil and grease by scrubbing the surface with commercial degreasers or floor strippers. If not, it will be necessary to physically remove the contaminated concrete layer.
4. Treatment of the Concrete Surface:
There are few methods for preparing the concrete floors including shot-blasting (grinding), scarifying and acid-etching. The intent is to remove laitance or any loose surface materials, as well as roughen the concrete surface. The standard recommends a surface profile appearance of fine (100 grits) sandpaper. Acid-etching is another method of treating surface.
6. Repairing the Cracks:
Once the floor is prepared as above and is dry, the next step is to address the holes and cracks. These have to be filled by a high strength epoxy structural repair gel (ZERA-BOND). The product has a butter consistency that is easily applied to fill any holes and cracks. Allow the epoxy to harden before proceeding with the application of the coating.
D. Application of Epoxy Coating:
1. Priming:
The concrete floor may need a primer coat. The purpose is to penetrate the concrete floor, seal it from outgassing, and act as adhesion promoter between the concrete surface and topcoat. Primers are thin-film systems less than 5 mils. The primer used may be either 100% solid (solvent free) epoxy, solvent-based or water-borne. In all cases, the two components have to be mixed thoroughly. Water and solvent-based primers are applied by brushes or rollers. For a 100% solids primer, they are applied by a flat squeegee and back rolled to ensure uniformity.
2. Coating:
Once the primer becomes firm to touch and tack-free, you may proceed with the application of topcoat as per product instruction.
E. Polished Concrete:
The basic premise of polished concrete consists of the following steps:
- Cutting the concrete with an aggressive diamond embedded pad until an even cut, called a "scratch pattern" is produced.
- Polishing the concrete starting with the highest level grit and ending up with the smoother level
- Densifying the concrete using sodium or lithium silicate to strengthen the concrete surface
- Polishing continues until the desired level of shine is achieved.
Benefits:
- Durability
- Low maintenance
- Repair and reuse of old slabs
- Improved reflectivity
- Noise
Just as densifying concrete increases its light reflectivity, it may also slightly increase sound reflectivity. Though EBN has not seen data to this effect, a polished, densified concrete floor may be acoustically brighter than a standard concrete floor, and it would assuredly be louder than a floor covered in a softer material, such as linoleum, cork, or carpeting.
Thermal conductivity
As with ceramic tile, terrazzo, and other concrete floors, polished concrete floors are more thermally conductive than most other flooring options. If not insulated beneath, the concrete slab floor may provide a significant conductive pathway for heat loss from a building, and it will reduce the mean radiant temperature (MRT) of a space, making occupants feel colder at a given air temperature. While this can be beneficial in the cooling season or when a building is being cooled, allowing the air temperature set point to be kept slightly higher, it does the same in the heating season, which carries an energy penalty—making it necessary to keep the air temperature higher. Even if a concrete slab is insulated underneath (and at the same temperature as the air), it can feel cool to the touch, leading to occupant discomfort and requiring a higher thermostat set point.
Fatigue
Like other hard-surface flooring, polished concrete causes fatigue for those who have to stand on it for long periods of time. Appropriate area carpets or mats should be used to avoid these problems.
- Energy savings - The reflectivity of the floor reduces the need for lightbulbs.
- Reduction in waste during installation - No carpet and/or tile trimmings
- Reduction in V.O.C.'s during installation - No mastic or solvent vapors being emitted
- Reduction in waste - Long-life floors don't need replacing
- Reduction in waste (again) - Polished concrete can be used by all tennants
- and other factors referring to reduced waste...
POLISHED CONCRETE IS ACID SENSITIVE.
If someone spills muriatic acid on your floor it will dull the finish instantly. Although it can be easily repaired, polished concrete should not be exposed to acids.
We don't recommend our floors in the following applications:
- Citrus Processing Plants
- Wine Manufacturing Plants
- Pickle Processing Plants
- Acid Manufacturing Plants
- Outdoor Applications ... Rain is normally acidic (5.4ph) and over time will dull
- Soft Drink Manufacturing
POLISHED CONCRETE IS NOT VISUALLY AS UNIFORM AS PAINT OR EPOXY
Sometimes you will see aggregate, sometimes not.
Sometimes you'll see darker areas. Sometime you'll notice "spider" cracking.